DX TODAY自社メディア
DX FrontLineコスモ石油の製油所デジタル化。三位一体(インフラ、セキュリティ、アプリ)で安全操業、安定供給を守る
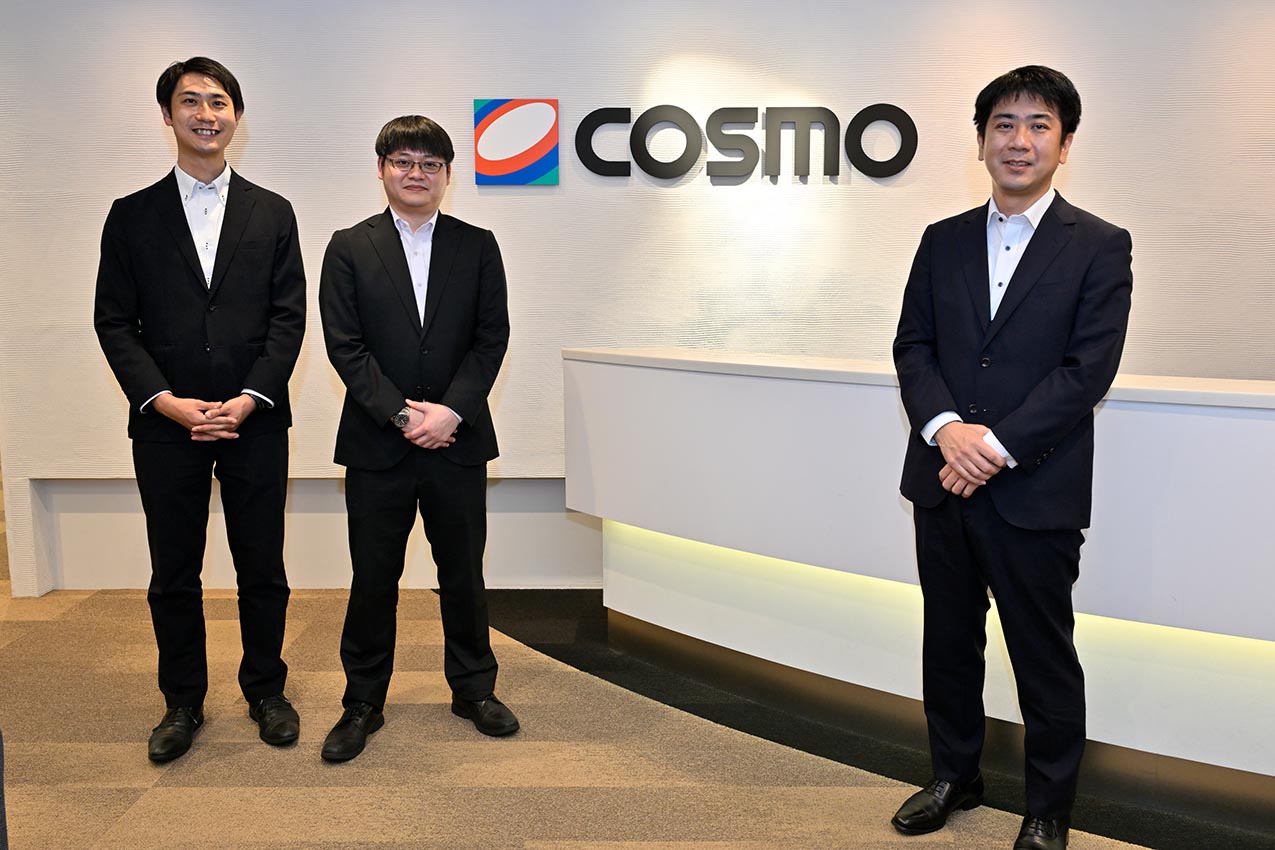
(中)製造技術部PJ・システムグループ 宍倉良徳さん
(左)製造技術部PJ・システムグループ 早瀬徹矢さん
早瀬 弊社では、プラントの異常の早期発見による設備稼働率の向上、より安全かつ効率的な職場環境の実現、さらには将来的な人口減少による採用難への対応として、積極的に製油所のデジタル化に取り組んでいます。10年後の働き方をイメージしつつ、センサー類を活用したデータ収集、AIによるデータ解析・意思決定の支援、いろいろな部署や事業所に点在しているデータの一元管理を進めています。さらにはバーチャル上に仮想プラントを構築し、場所にとらわれない効率的な働き方の実現も視野に入れています。
伊東 私たちの現場となる石油精製や石油化学のプラントは24時間常に稼働しており、日中のみ動かして夜間は止めるといったことができません。一度止めてしまうと再稼働に数日間かかってしまう設備もあります。止めないことが原則ですから、設備の不具合による突発的なプラントの停止を未然に防ぐための巡回点検は重要です。製油所は広い敷地に様々な設備があり、運転員が巡回しながら機器の点検を行って異常やその兆候がないかを確認しています。点検は五感に頼るところもあって、ベテランの運転員は現場機器の音や異臭で異常を察知することもあります。こういったノウハウの数値化や不具合の予兆段階での把握を目指したいと考えています。
災害時にも使える
強固な通信インフラの構築
早瀬 今後、プラントの現場で様々なスマートデバイスを活用していきたいと考えていますが、そのために通信環境の整備が非常に重要と考えています。通信環境はいわばインフラです。
伊東 製油所には計器室と呼ばれる建物が点在し、そこで装置の稼働状態をモニターしながら、プラント内を流れる油の流量の増減や温度の上げ下げなどの操作を行います。これらの操作はプラントで点検作業を行っている担当者と連携して、現場の作業と計器室の操作を連動させながら実施し、プラントを稼働させています。計器室と現場とは無線機を使い音声でやり取りしていますが、画像や動画を含めた情報の共有を進めており、そのために通信環境を刷新していく予定です。
早瀬 携帯電話で代替するという議論もありましたが、大きな地震の際にはキャリア(公衆回線)がつながらないことを私たちは経験しています。災害時に現場と計器室の通信不通はあってはならないことですから、自前の通信網を整える方向で進めています。
伊東 製油所専用の携帯の基地局を建てるイメージですね。今後、現場と計器室のやり取りはスマートデバイス等で行う想定であり、これらが災害時にも使えるような通信インフラを構築したいと考えています。
人手不足を補う
歩行ロボットの実証実験
早瀬 先述したヒトがパトロールしているプラントの点検ですが、代替を見据えて4足歩行ロボット活用の検証を始めています。稼働中のプラントでは利用条件等のハードルが高いため、休止中の設備を利用した実証実験を行いました。プラント内には狭い場所や、計器が高い位置に付いているところもあります。まずはロボットを歩かせたところ、階段の上り下りや障害物の回避、計器類の撮影などが行えることを確認しています。ロボットは、まさにリードのない犬のように動きます。重量もあるので、安全対策は1つの課題です。
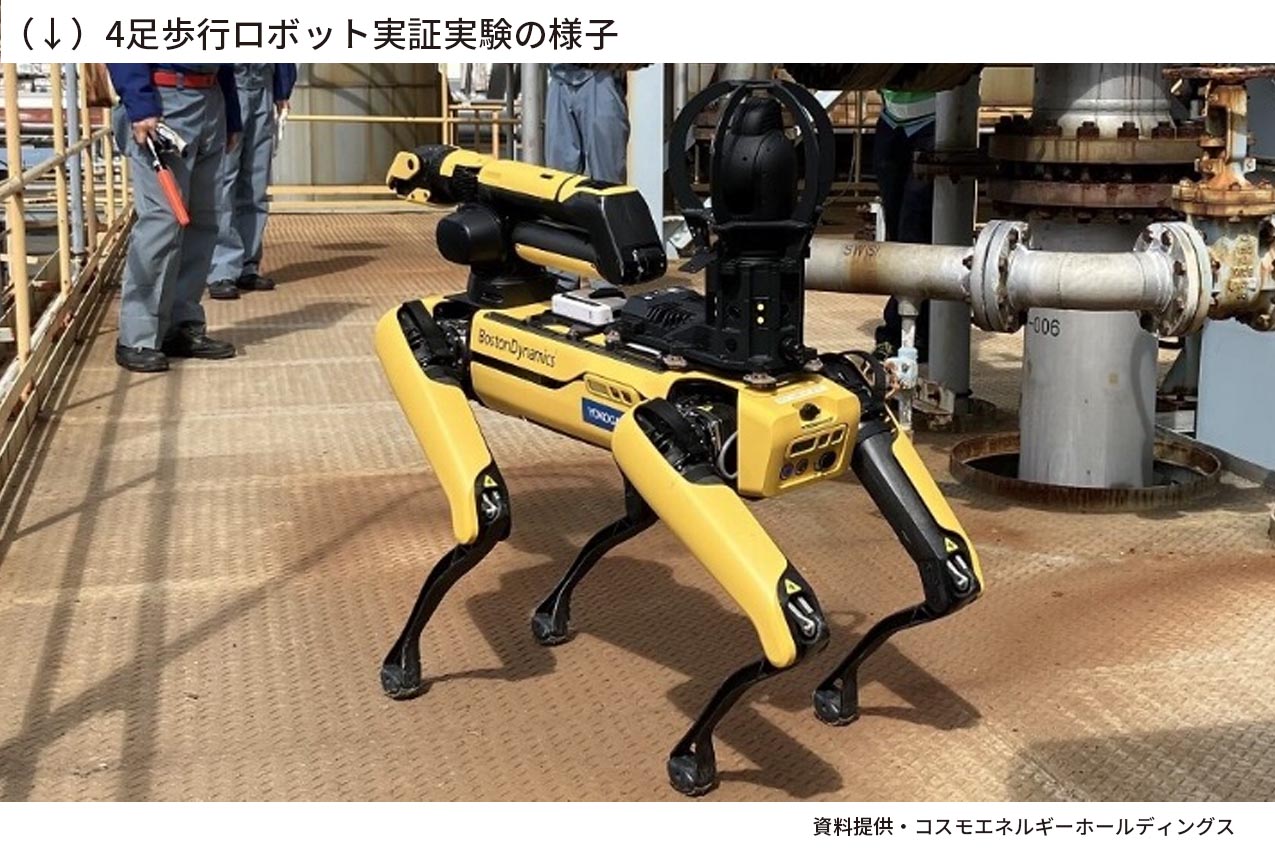
伊東 4足歩行ロボットは移動するためのツールです。そこに何を載せるかがとても重要で、カメラの他にマイク(音)なのか温度計なのか、それともガスの検知器なのかと、搭載するセンサーを検討している段階です。また、カメラで撮ることはできても、その解析をどうするかという技術的な検討も必要になります。さらに、クリアしなければならないのが、危険物を取り扱う現場でロボットを使うことに対しての、法を含めた運用環境の整備です。製油所内は大量の可燃物を取り扱いますので、プラントには着火源になるようなものを置かないことが原則です。ですから、プラントで利用する電気機器には火花が出ないような特殊な対策をしています。
早瀬 実証実験中のロボットは、そういった対応をまだ取れておらず、仮にそのような対応を取ると重たくなるなど、使いにくくなってしまうため、今後詰める必要があります。
伊東 また、夏場のプラントは非常に暑くなります。石油精製では原料となる原油を300〜400度という高温に熱し、沸点の差を利用して蒸留したり、不純物を除去したりするプロセスになっているため、常に熱気に溢れています。そこに昨今の猛暑ですから、現場も夏場の熱中症対策に苦労しています。ヒトの安全は最優先課題ですから、ロボットを使っての現場点検は、1つの手段としてとても有効だと考えています。
システム化に並行した
セキュリティ対策
宍倉 日本国内でも大手企業がサイバー攻撃を受けるなど、セキュリティ対策は喫緊の課題です。日本では2014年にサイバーセキュリティ基本法が施行され、石油業界は国民生活の重要な社会的基盤を担う企業として指定されています。つまり、サイバーセキュリティにきちんと対応し、万が一サイバー攻撃を受けたとしても石油製品の供給を継続していくことが求められています。
伊東 プラントの中では、ポンプを使って油を送り続けています。その量を減らしたり増やしたりといった制御を行いますが、その制御装置が長い時間の中でシステム化してきました。以前は制御専用の機械がありましたが、今はパソコンの画面上で数字を打ち込むと、自動的に流量を変えてくれます。システム化により効率的になった一方で、サイバーセキュリティのケアも必要になっています。
宍倉 そうした中で、制御装置を作ったメーカーでないとわからない部分が多々出てきます。そういったところはメーカーときちんと情報交換をして、議論をしながら対策を進めているところです。少し前までは、制御システムに対するセキュリティ対策は、ウイルスやクラッカーに侵入されないように、という思想でやっていました。ところが近年では、完璧に侵入を防ぐのは難しくなってきています。ですので、サイバー攻撃を受けたとしても、それを見つけて対応できる、あるいは被害を広げない。もし障害が出たとしてもすぐに復旧できる、そういった体制を整えています。プラントの制御システムは基本的に外部とつながっていないので、直接サイバー攻撃を受けることはありませんが、平時から万が一に備えた対応を進めています。
伊東 弊社は燃料油やLPガスなど大量の危険物を扱っています。そのため、いろいろな法令を遵守しています。その中の1つに高圧ガス保安法という法令がありますが、高い保安力を有すると評価された事業所に対し、一定の権限を持たせる「高圧ガス保安法における新認定事業者制度」が始まり、2024年8月に、弊社堺製油所は第1号となるA認定を受けました。この認定の要件にはテクノロジーの活用やサイバーセキュリティ等のリスク対応も含まれており、弊社の取り組みについて評価いただいたと感じていますが、これに満足することなく、さらに上を目指していきたいと思います。
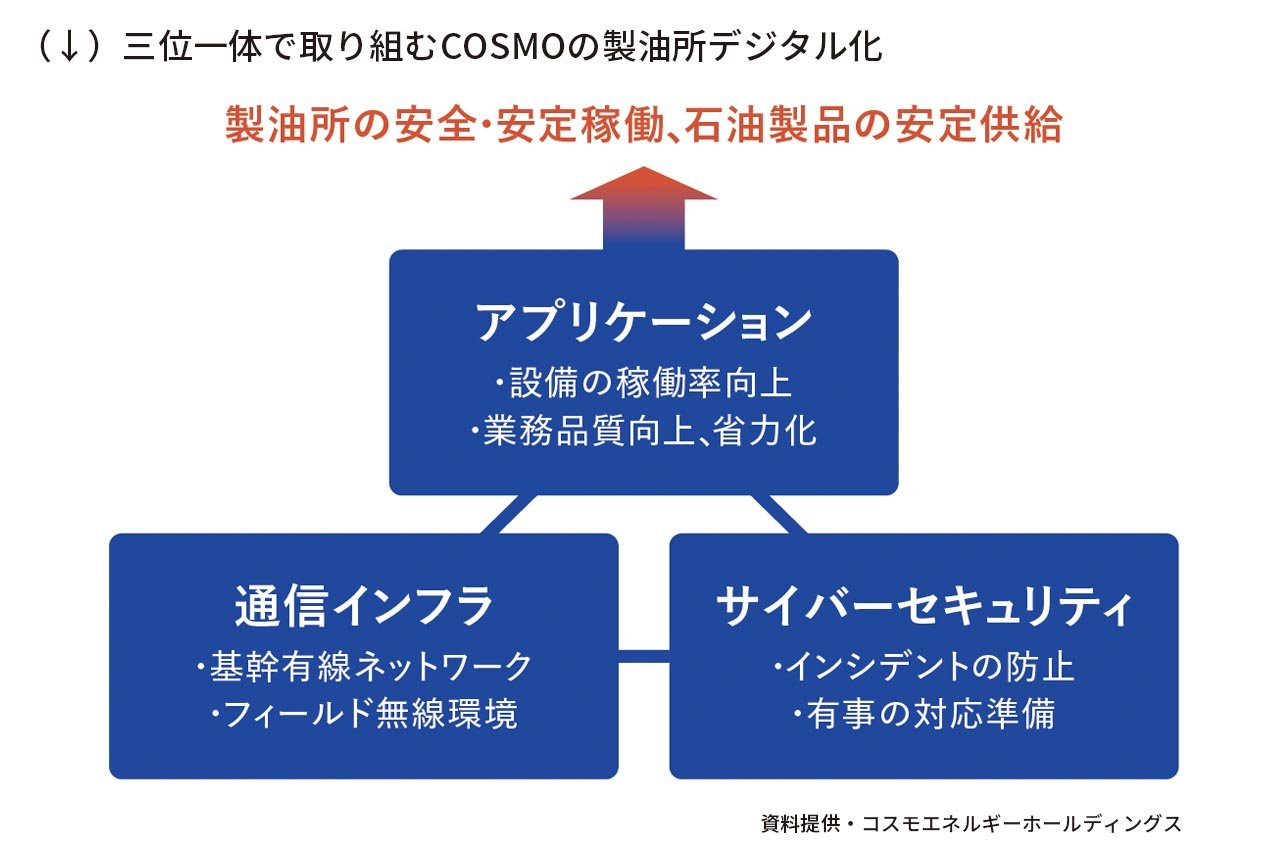