DX TODAY自社メディア
DX FrontLine1デジタルツインと経営シミュレーションのダブルで取り組む徳山製造所
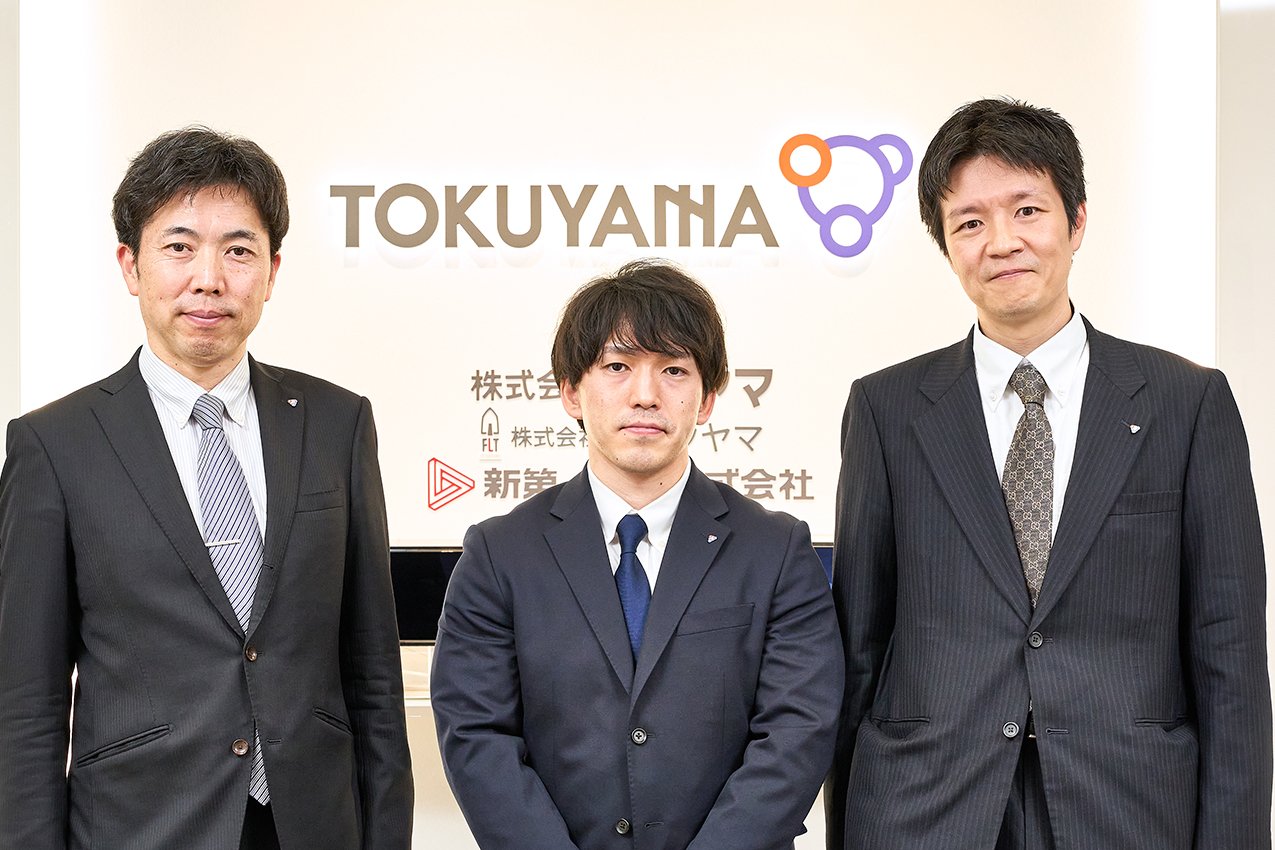
(中)株式会社トクヤマ 生産技術センター 兼 ITソリューショングループ 主任 今井俊輔さん
(右)株式会社トクヤマ 生産技術センター 主任 山下義晶さん
立川 弊社は化学品やセメントを始め、電子材料からライフサイエンスに至る様々な事業を展開しています。私たちが所属する生産技術センターは、これらの研究開発から事業化までを化学工学の専門家として技術検討するのが主な業務です。
山下 流体を扱うことが多いですね。分離や特定の成分を抽出するといったプラント操作になるのですが、これまでは1990年代に導入したプロセスシミュレーターを使ってプラントの挙動評価を行っていました。
2017年にあるフォーラムに参加し、デジタルツインがシミュレーターで作れると耳にしました。しかも他社ではすでに取り組みが始まっていると知り、危機感を持ったのが導入に至ったきっかけです。
立川 当時の弊社では、設計用途としての使い方がメインであり、検討の対象は主要機器とその関連機器くらい。プラント全体での検討は行っていませんでした。生産性を向上し、利益を増やそうとするとプラント全体の効率化が必須であることは言うまでもないことです。
山下 早速翌年から、プロセスシミュレーターでデジタルツインを作り始めたのですが、まず、必要な情報を収集しなければなりません。その情報はというと、部署ごとに保存方法が異なり、電子化されていないものが多数あるばかりでなく、中には文書化されていないノウハウや属人化されている情報があって、個人から直接聞き取るなど、情報集めに膨大なエネルギーが必要でした。
それらに加え、当初から使っているプロセスシミュレーターではデジタルツインを構築する上での機能が十分でないことが分かり、3年かけて新しいものに全て移行しました。ファイルの置き換えはもちろん、ユーザーも新たに使い方を習得しなければなりませんでした。
立川 この作業は大変でしたが、社内に培われてきた情報を集約し、シミュレーター上で再現できるようになることで、得られたノウハウを新規事業の検討に活用するなど、大きな意義があったと思います。
山下 デジタルツインを活用することで、運転支援や設計面でのボトルネック解消に向けた検討が可能になります。
また、実績のない運転条件の場合は、外挿性を担保するため実機を忠実に再現する必要があり、プラント運転データを使って精度を上げる取り組みも行っています。デジタルツインは物理理論に基づいたモデルで構築されるので、経験知を理屈で示すことができるようになり、若手エンジニアの教育にも役立ちます。
立川 安全と品質の面でもメリットがありますね。実際のプラントでは大きく条件を変えて運転すると、事故や不良品の発生につながる懸念があります。ですが、デジタルツインを使えば、コンピューター上のプラントであらゆる検証を重ね、確認してから実機への導入が可能です。
経営シミュレーションを
同時に行い、全体を最適化
今井 このデジタルツインでの効率化に加え、経営視点で徳山製造所全体を効率的に運用できるよう、弊社で取り組んでいるTDX(=Tokuyama DX)の一環として、経営シミュレーションモデル「T-FORCE」を新たに構築しました。企業価値の向上や環境に対応したベストな運営方針を提案するツールです。
立川 徳山製造所では、各製造ラインが高度に統合されています。そこで、エネルギーや原料、廃棄物循環などのバランスを取りながら、CO2排出量やICPなどの条件を考慮した様々なパターンを予測計算することができるようにしました。
今井 この「T-FORCE」は着手から検証まで含めて約半年で完成させました。デジタルツインもそうですが、現場での操作画面の使いやすさにこだわって作り、誰もが使い慣れたExcelと同じような使い勝手にしています。
立川 発電所やシリコン、電解などの巨大プラントでは効率を数%上げるだけでもコストは大きく変わります。また、弊社では現在、事業ポートフォリオの転換や地球温暖化防止への貢献を進めるにあたり、大きな変化が求められています。デジタルツインと「T-FORCE」という2つのツールを使って、様々な改善を進めて行きたいと考えています。
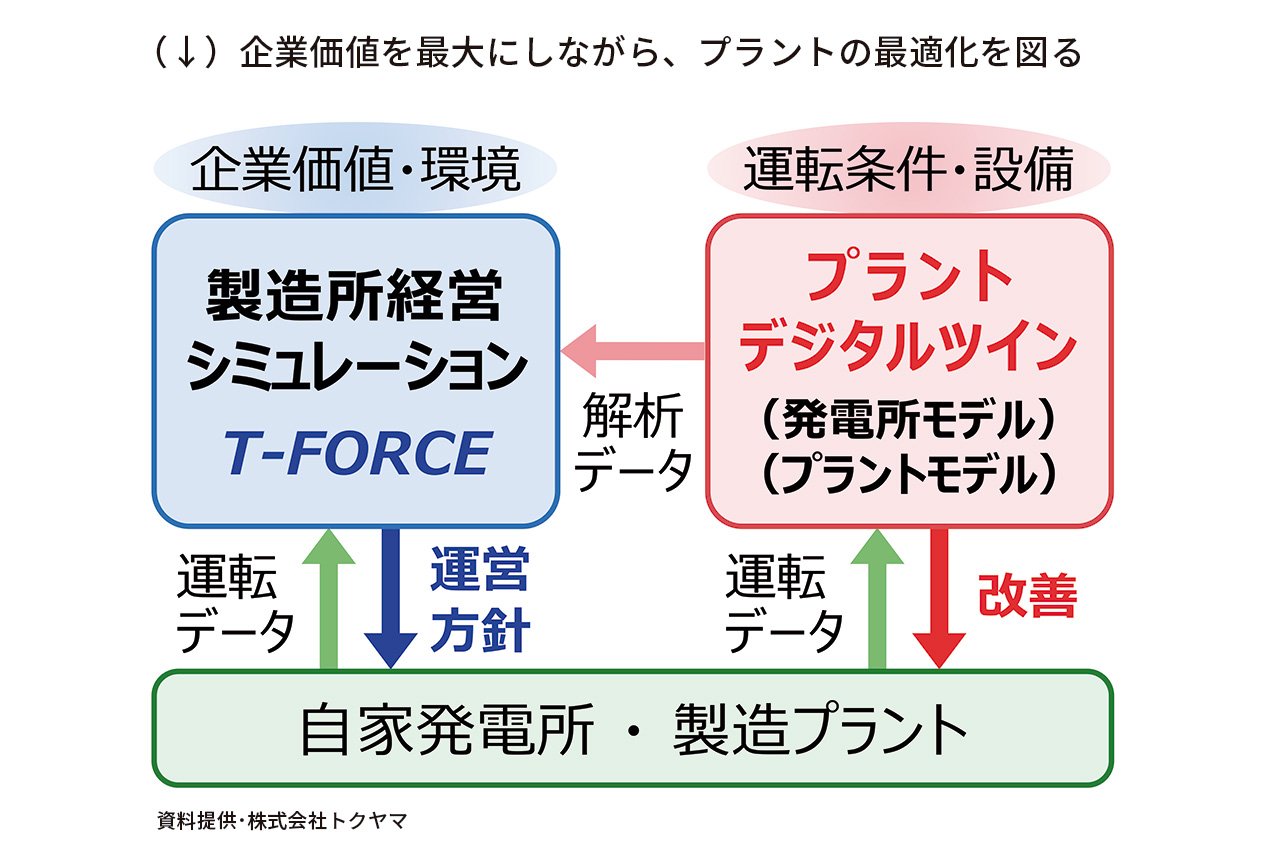